This collaboration between a leading manufacturer of space solar technology and acp systems has resulted in an innovative solution for the automated loading and unloading of solar wafers onto workpiece carriers. The robotic system, supported by image processing technology, ensures precise positioning of the wafers within the carriers, compensating for both manufacturing tolerances and shrinkage caused by cooling. With its ability to address these challenges, this technology offers significant advantages for the solar industry.
Table of Contents: What awaits you in this article
Innovative Solution for Automated Loading and Unloading of Solar Wafers
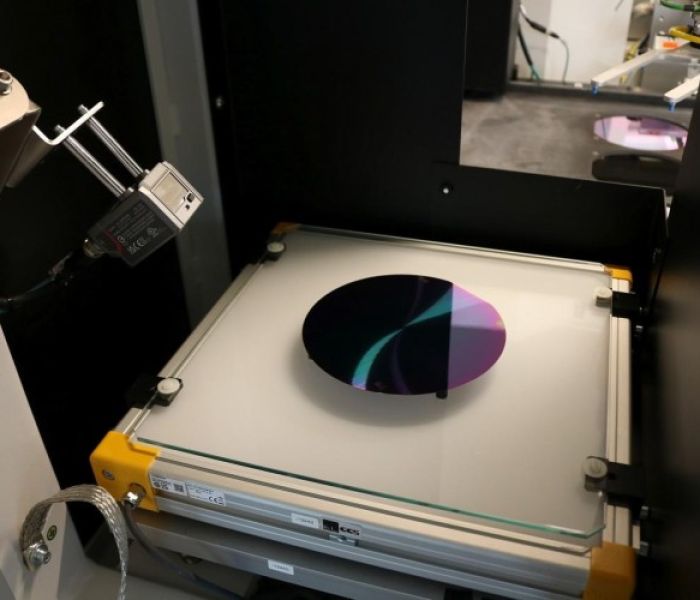
Das Kamerasystem über dem hinterleuchteten Ausrichttisch (Foto: AZUR SPACE)
The automation of the loading and unloading process for solar wafers presents a significant challenge due to the need for precise positioning within the carriers to prevent potential damage. Additionally, it is crucial to compensate for manufacturing tolerances and the shrinkage caused by cooling. Fortunately, these challenges have been successfully overcome through the implementation of acp systems’ image processing-based robotic solution.
Innovative Robotic Solution Ensures High Precision Positioning of Solar Wafers
The robotic solution developed by acp systems utilizes an industrial robot equipped with a specialized flat vacuum gripper system. This robot effectively extracts solar wafers from cassettes and carefully places them onto a backlit alignment table. Through a high-resolution 12-megapixel camera system, the precise position of each wafer is detected and transmitted to the Cognex Vision Pro software. Based on this information, the system calculates and communicates the necessary compensations for both position and angle, ensuring exceptional positioning accuracy.
Integration of Flippstation enables efficient and precise handling of solar cells
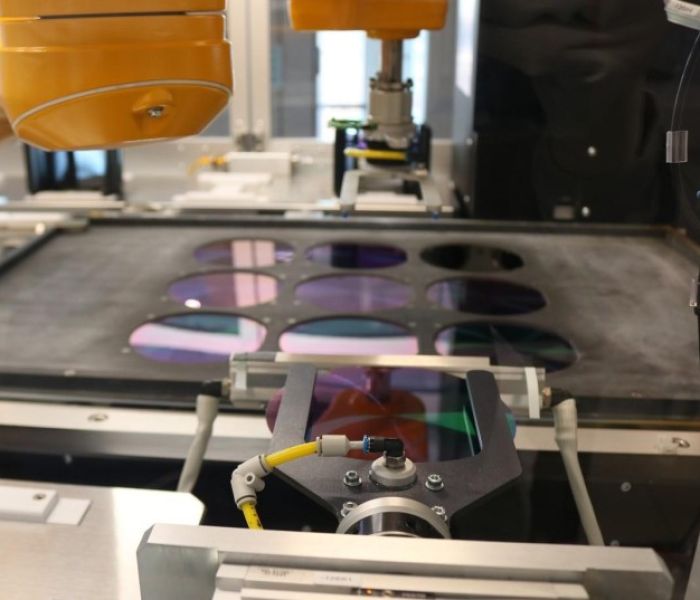
Für das Drehen beidseitig zu beschichtender Solarzellen (Foto: AZUR SPACE Solar Power)
A flip station has been integrated to rotate solar cells that are coated on both sides. This station receives the wafers individually from the robot and rotates them by 180 degrees. Afterwards, the robot takes back the wafer and transports it to the alignment table. This integration enables an efficient and precise processing of the solar cells.
Camera-based quality control ensures defect-free edges of solar wafers
After the coating process of the solar cells, a final quality control is performed by the camera system at the alignment table. It checks if the edges of the wafers are free from damages. This integrated quality control ensures the product quality.
Innovative Robotic Solution by acp systems Ensures High-Precision Solar Wafer Processing
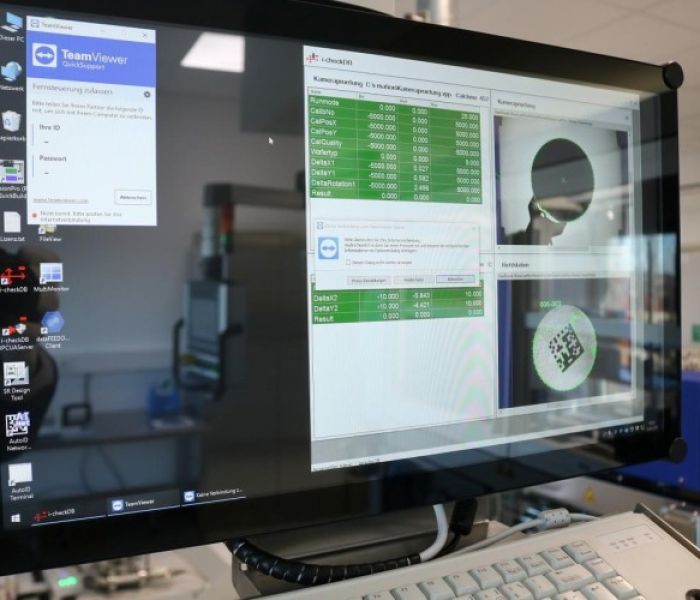
Vor dem Ablegen der beschichteten Solarzellen in den Kassetten (Foto: AZUR SPACE Solar Power)
The innovative image processing-based robotic solution developed by acp systems ensures precise and gentle handling of solar wafers, significantly reducing the risk of breakage. Since its implementation, there have been no handling-related wafer breaks, demonstrating the system’s reliability. The automation provided by this fully automated system greatly enhances productivity and cost-effectiveness, making it a valuable asset for the solar industry.
Innovative Robotic Solution Enhances Solar Industry Efficiency and Quality
The development of an image processing-based robotic solution for the automated loading and unloading of solar wafers offers numerous advantages for the solar industry. By precisely positioning the wafers and compensating for manufacturing tolerances and cooling-induced shrinkage, the product quality is improved. Furthermore, the automation of the process enables increased productivity and cost-effectiveness. The robotic solution by acp systems represents a significant step towards more efficient and sustainable solar production.