Focused on efficient production supply, high automation levels, and ergonomic workstations, the new logistics center built by family company Wildeboer with Unitechnik introduces an automated storage system at the Weener headquarters. It automates intralogistics workflows, reduces manual handling, and expands floor area across three levels for additional assembly. It provides scalable capacity. Designed to support future growth, this infrastructure integrates advanced material flow technologies to boost throughput and operational flexibility.
Table of Contents: What awaits you in this article
Automated System Overcomes Storage Challenges, Boosts Production Efficiency
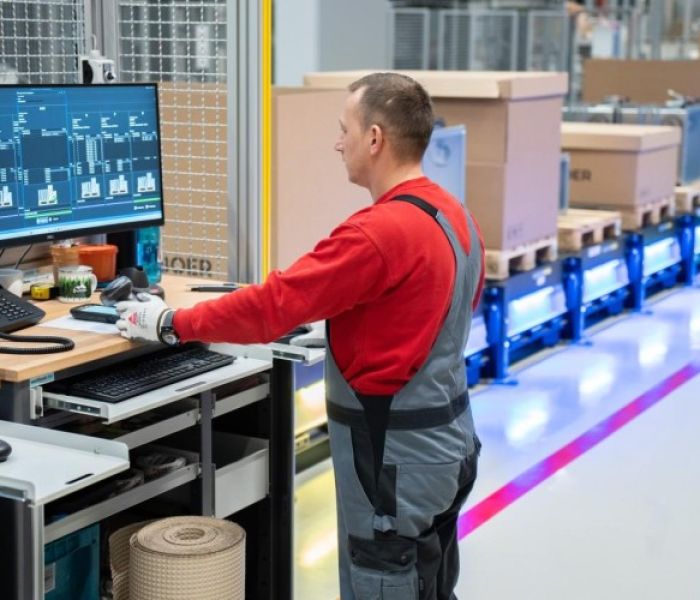
Farbige Leuchtanzeigen für Mitarbeiter (Foto: Unitechnik)
At Wildeboer, insufficient warehouse capacity resulted in large volumes of materials being stored across decentralized manual storage areas and temporary staging locations. To address this challenge, automating material handling workflows became essential to consolidate operational zones and adopt a goods-to-person approach. A centralized automated storage system was introduced to minimize manual handling and create extra floor space for expanded assembly operations as well as new production areas supporting future growth.
A Comprehensive Logistics Concept for Wildeboer and Unitechnik
Working in tandem, Wildeboer and Unitechnik created a logistics architecture that segregates manufacturing and storage zones while adding 10,500 square meters of warehouse space. Built on Unitechniks deep process expertise and vendor-neutral, solution-focused planning, this approach ensures an adaptable framework. Key processes emphasize modular scalability and robust systemwide reliability. From material inflow to outbound shipping, operational step is streamlined. The design supports uninterrupted production supply and expedient distribution, boosting throughput.
Efficient Logistics Hub Boosting Production Efficiency and Automation
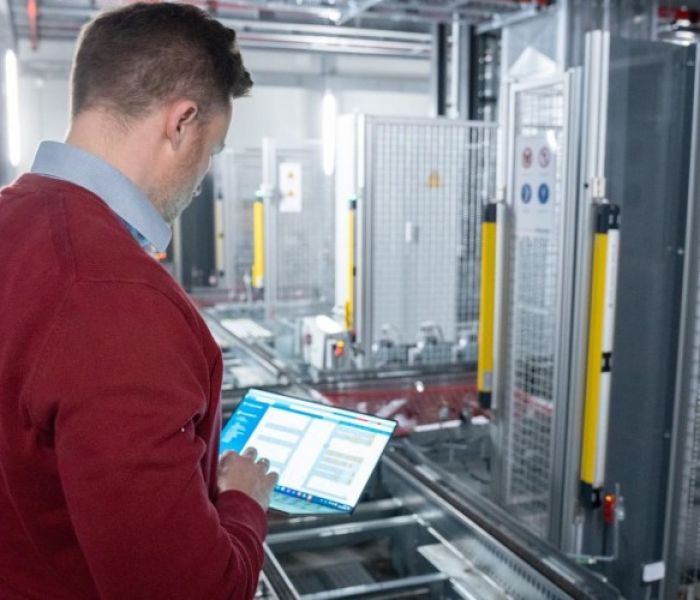
Die stufenlos zoombare Anlagenvisualisierung (Foto: Unitechnik)
This logistics center by Wildeboer and Unitechnik includes a three-aisle high-bay warehouse for Euro pallets and mesh boxes plus an automated small-parts storage area for KLT containers. Combined pallet and container picking stations prepare materials for production and customer orders. The UniWare management system coordinates all material flows and inventory movements, while driverless vehicles guarantee efficient transport. It also integrates autonomous cleaning robots and a VDA 5050-compliant fleet management platform.
A high-quality collaboration between Wildeboer and Unitechnik
Collaboration between Wildeboer and Unitechnik demonstrates high technical standards and a partnership approach. Incorporating features such as a pallet inspection system and the UniWare warehouse management software, the logistics center achieves exceptional quality and operational efficiency. Despite the disruptions caused by the COVID-19 pandemic, the project reached completion on schedule. This success resulted from proactive communications, rigorous planning, and well-coordinated teamwork between all stakeholders, ensuring seamless execution under challenging circumstances.
A long-term partnership for continuous warehouse optimization at Wildeboer
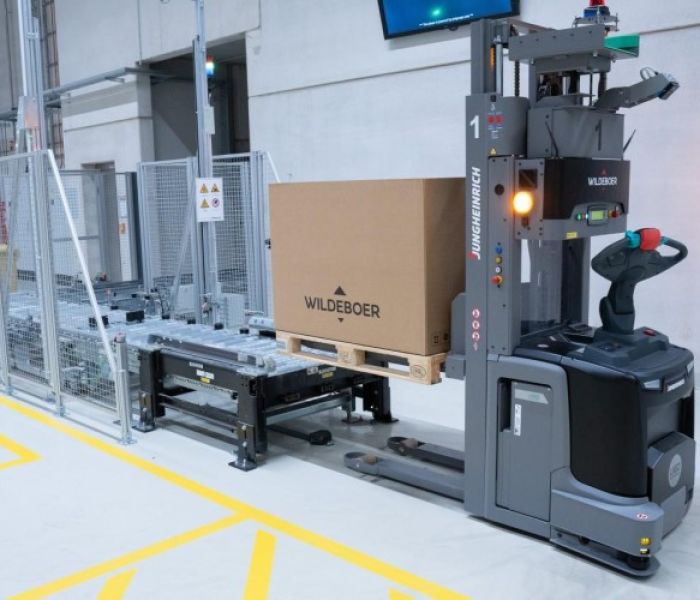
Gefertigte Bauteile werden über FTS-Fahrzeuge transportiert (Foto: Unitechnik)
Beyond project completion, the collaboration between Wildeboer and Unitechnik remains active, focusing on identifying and implementing continuous improvement opportunities within the warehouse. As a lifetime partner, Unitechnik provides round?the?clock support to ensure the logistics centers overall sustainable performance. This partnership relies on proactive planning and seamless communication to drive ongoing enhancements. Consequently, warehouse operations are constantly optimized, contributing to significantly increased efficiency and productivity for Wildeboer throughout all operational phases.